Leak Testers
Leak Testers
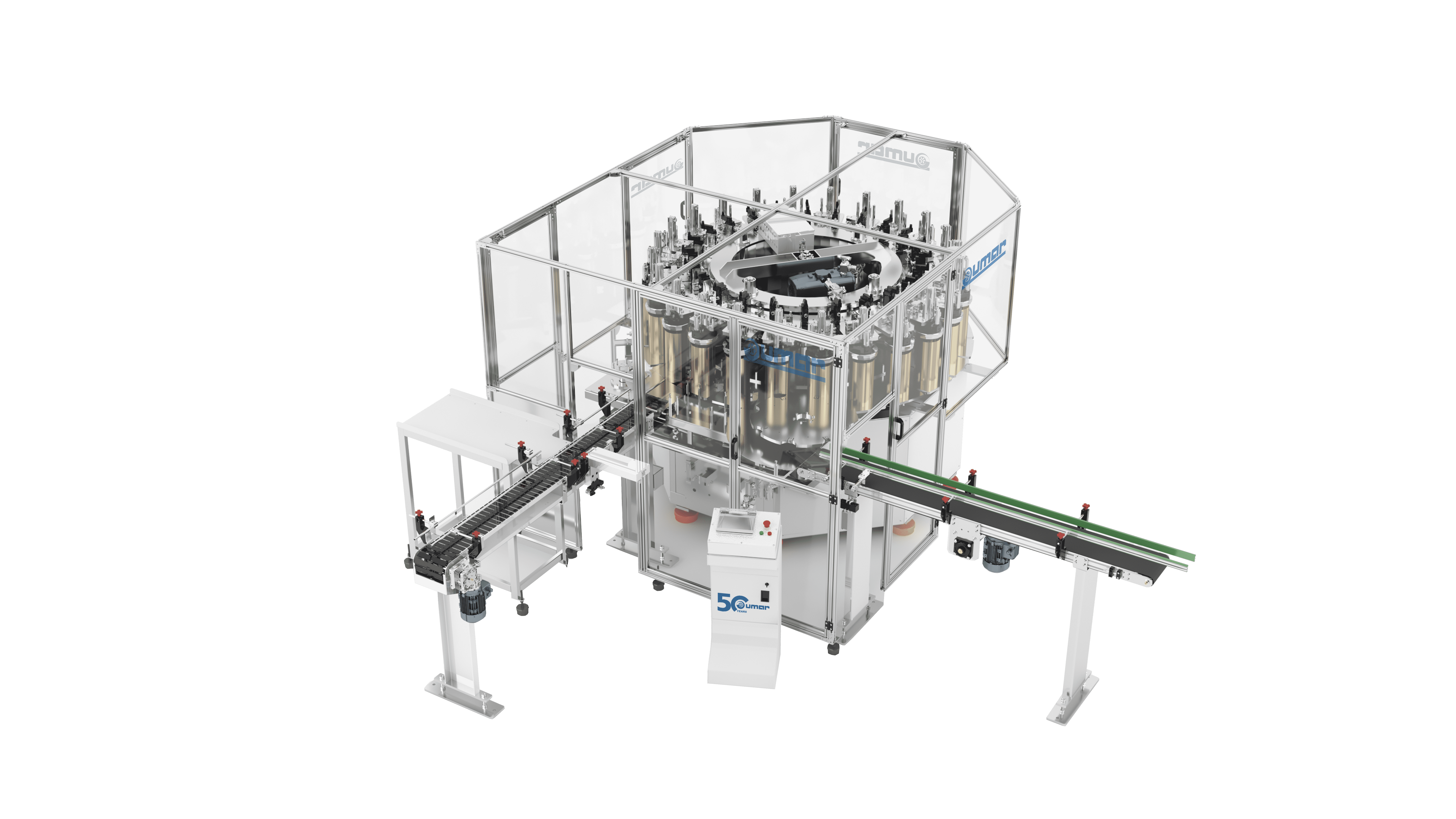
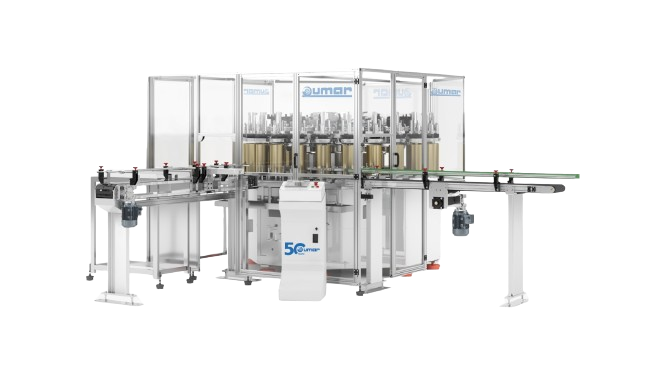
Welcome to Umar Makina Co.
Founded in 1972 in Istanbul, UMAR MAKINA has become a benchmark in modern Turkish industry by exporting the first Turkish-made machinery. Today, we specialize in tin can manufacturing turn-key lines and automatic stand-alone machines, designed to meet the highest global standards. With 85% of our annual production exported worldwide, our Industry 4.0 compatible smart production lines transform manufacturing into intelligent, data-driven operations—offering real-time access through advanced software and integrated automation technologies.
Stay up to date with the world of business and tax with news, insights and articles from our expert editors, accountants, and advisors. Our professionals provide valuable perspective on a range of topics that can help inform your business decisions and keep you informed about industry trends.
Eco-Friendly Metal Packaging
At UMAR MAKINA, we believe in a cleaner future with our motto: "metal recycles forever."
Metal packaging is the ultimate choice for sustainability. It can be recycled endlessly, creating zero waste and leaving a minimal carbon footprint. By choosing metal, you're not just selecting a reliable packaging option—you're supporting a healthier planet.
At UMAR MAKINA, we offer a unique opportunity for those eager to expand their knowledge and make a meaningful impact. Our commitment to innovation drives us to apply cutting-edge techniques in our in-house production facilities, creating an environment that feels like an engineer’s playground.
Here, you’ll have the chance to engage in every aspect of machine production, working alongside a dedicated team united by a common goal: to create enjoyable, transformative solutions for the industry.
If you’re ready to take your skills to the next level and give back through collaboration and creativity, we invite you to join us. Experience the vibrant life at UMAR, where your contributions help pave the way for a brighter future!
Connect with our expert Purchasing and Sales Marketing Engineers, or reach out to our R&D Engineers to discuss your project needs. We are here to listen and understand your goals, providing personalized, cost-effective solutions tailored to maximize the benefits of your machinery and production line services.
Let us be your partner in driving your success forward. Together, we can turn your vision into reality!